

performed an experimental investigation into the effects of joint thickness, laminate taper, and missing fasteners on load distribution of single-lap, multi-bolt, countersunk composite joints. The effects of ply property and ply stack on stress distribution were observed and discussed. proposed an analytical method to calculate stress around interference fit holes on composite pinned plates under tensile load. They found that increasing bolt torque on the outer bolts can balance the load distribution while the by-pass stresses also played a significant role in controlling joint failure. proposed a simple analytical approach for modeling the non-linear elastic behavior of three-bolts composite joints.

Researchers have done a lot of research to analyze and optimize the rivet/bolt load distribution in composite joints. However, the load carried by individual rivet is different because of the various distances from the position where the load is applied. In practice, multi-riveted lap joints are commonly used to meet the strength requirements of aircraft components. It is concluded that both the increase of squeeze force and initial fit tolerance can lead to an increase in residual stress. studied the residual stress distribution in a plate concerning the influence of initial fit tolerance and the squeeze force. It was found that residual stresses beneath the rivet head were influenced primarily by through-thickness compression of the joined sheets. built a 3D finite element model of installation rivets in the monolithic aluminum sheet. The results showed that sealant can increase residual hoop stress in most cases. established a three-dimensional finite element model of the riveting process to determine the effects of interference and sealant on the residual stress state. The fatigue performance of interference-fit riveted joints can be effectively improved because of residual stress. The interference fit provided by rivet expansion introduces the residual stress around the riveted hole.
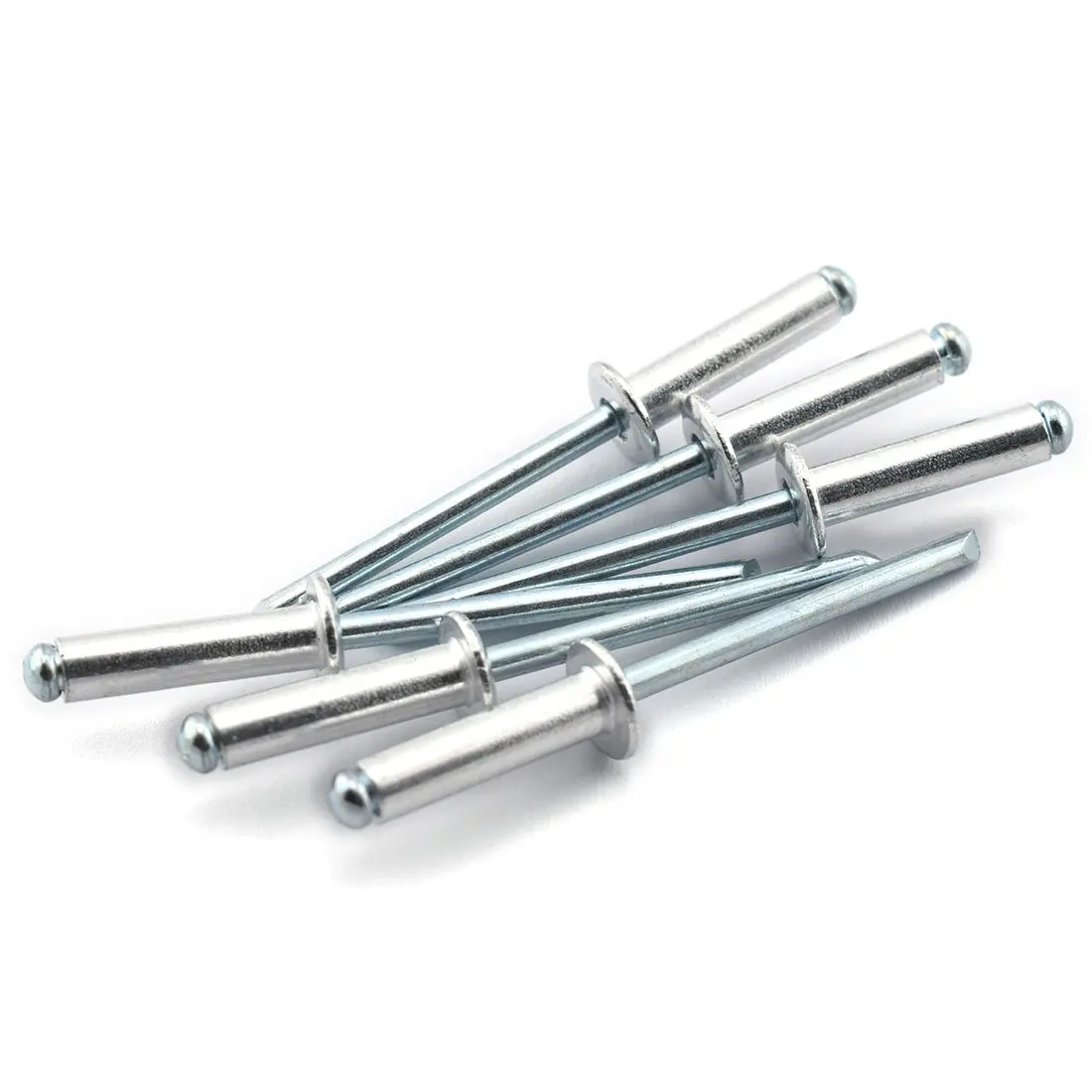
Therefore, it is very necessary to analyze, estimate, and enhance the fatigue performance of riveted joints. The fatigue life of riveted joints is an essential factor affecting flight safety and aircraft service life. In aircraft manufacturing, riveting is widely used because of its reliability, easy operation, and low cost. These aircraft structures are often joined by riveting, welding, bolting, or hybrid joining technologies, which is a unique challenge in terms of joint reliability, strength, and cost-efficiency. To make the air traffic sustainable, the lightweight components made of aluminum alloy, titanium alloy, or fiber-reinforced composites have been widely used in aircraft manufacturing. With the rapid development of air traffic, fuel consumption and CO 2 emissions are becoming a growing concern in the field of environmental protection. Based on the simulation and experimental results, a good combination of structural parameters of the riveted lap joint is found which can optimize the stress distribution around the riveted hole and improve the fatigue life of the riveted lap joint. Finally, the fatigue tests are conducted with riveted lap joint specimens to verify the theoretical model and FE results, and a good agreement is observed. The influence of rivet diameter and pitch on stress distribution around the riveted hole are discussed. Then, the finite element (FE) model of riveted lap joints are established. The rivet-load stress, bypass stress, and interference stress around the riveted hole are analyzed. First, a theoretical model of the riveted lap joint under tensile load is developed by using the spring-mass model. In this paper, the fatigue performance of the riveted lap joints with various rivet diameters and pitches are studied based on stress distribution analysis under tensile load. The fatigue performance of riveted joints has a significant impact on the service life and reliability of aircraft. Interference-fit riveting is one of the most widely used mechanical joining ways in aircraft assembly.
